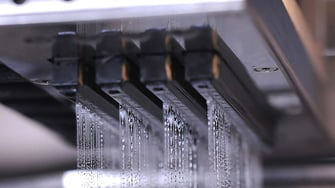
Metal Binder Jetting Technology Characteristics
Many different types of materials can be used in metal binder jetting. DSB is exploring applications involving stainless steels, low alloy steels, specialty alloys, and reactive materials, among others.
Metal binder jetting is used to create designs with nearly limitless 3D complexity possibilities, including:
- Geometries not previously possible or economically feasible
- Greater complexity and better surface finish/feature details compared to investment casting designs
- Ability to combine multiple parts into one
- Geometries that are difficult to produce in hard tooling
- Labeling: partner numbers, names, and logos
- Internal structures (channels, cavities, etc.)
- Internal undercuts
- Holes of any shape at angles to one another
- Minimum printed hole size: 1.5 mm
- Bracing structures to provide extra part strength
- Light weighting: only putting material where needed
- Support structures help manage sintering shrinkage and distortion
Metal binder jetting can hold the dimensional precision of +/- 0.75% printed; +/- 1.0% sintered and a minimum wall thickness of 1.0 mm, depending on part geometry and green strength after printing. No tooling is required.
Learn more information on our metal binder jetting products.
What is Metal Binder Jetting?
Metal binder jetting is an additive manufacturing process that involves applying a liquid binder onto a thin layer of metal powder particles using inkjet print heads to create a solid part. The process is repeated layer by layer, using a digital design file as a map, until the object is complete.
After printing, metal binder jetting parts are placed in a cure oven. During the curing process, they are heated up, generally from 100-200c, to initiate the polymerization of the binder. This allows the “green” - or unsintered - part to be handled and removed from the print bed and de-powdered. After de-powdering, the parts then undergo high temperature sintering to fuse the metal particles together and reach the part’s desired properties.
The Massachusetts Institute of Technology (MIT) first developed the binder jetting process in 1993, but the technology didn’t really take off until 3D printing emerged as a viable manufacturing process for mass production in the early 2010s. Binder jetting can utilize materials other than metal, such as sand, silica, and polymers.
A wide variety of 3D printing technologies are available, many utilizing lasers or nozzles that require a lot of material and multiple manufacturing steps. This drives up costs and increases build time. Metal binder jetting, by contrast, offers some distinct advantages:
- Materials are more affordable and easily recycled
- Quick print speeds enable high-volumetric output
- High-quality, functional parts are created
- Complex geometries not previously possible through traditional manufacturing are easily produced
- Repeatability makes metal binder jetting competitive with traditional mass production processes
Metal binder jetting is up to 10x more economical than other 3D printing processes and provides extremely fast and scalable production, making it a cost-effective, highly customizable solution for volume production of precise metal parts.
Metal Binder Jetting for Mass Production
Additive manufacturing involves the use of CAD software or 3D scanners to slice the part together, layer by layer, to create a solid object. It’s the opposite of subtractive manufacturing, which involves removing material from solid mass to achieve the final desired shape.
Metal binder jetting is faster and cheaper than other additive manufacturing methods and offers greater design versatility, as well as scalability. This makes it a flexible and economical solution for mass production. Benefits include:
- Shorter Lead Times. Transitioning a design concept into a validated, production-ready part often takes weeks with traditional manufacturing. That timeframe can be reduced to a matter of hours with additive manufacturing technology. Because metal binder jetting is software-based, design changes can be made the same day without tooling.
- Multiple Assembly Consolidation. Metal binder jetting is the perfect solution for mass producing complex and lightweight metal parts. Multiple layers of parts can be stacked atop one another and housed within all three dimensions of the build box, making it easy to manufacture multiple parts at once. The usage of lattice structures — repeating patterns that connect to form 3D shapes — means fewer parts are needed for assembly. and labor costs can be significantly reduced.
- Long-Term Savings. While a metal binder jetting system may cost more to set up initially, you have to take into consideration your total cost of ownership (TCO). Over time, your investment will save you money. Materials are more affordable and easily recycled, saving you money with each production run. Fewer materials and faster print times mean you’ll spend less on labor, as well. Reduced lead times, less waste, and better flexibility all translate to a lower TCO in the long run.
Fast speeds, material flexibility, and the ability to replicate complex, intricate designs precisely and efficiently make metal binder jetting a threat to traditional mass production technologies.
The Metal Binder Jetting Process Explained
The binder jetting process is the most promising metal additive manufacturing technology to industrialize serial production of complex, functional powder metal parts. It involves the following steps.
- The customer supplies us with a drawing of the part, which we optimize for metal binder jetting.
- Once the design is finalized, the CAD format is converted to an STL file and transferred to our printer via USB.
- When the build box has been created, a technician loads the format and begins the print. A heated lamp moves over the powder to dry the binder and maintain the temperature of the print bed.
- Powder is dispensed on the print bed and a flat plane is rolled across the print bed. The print head travels over the print bed, dispensing binder over the part geometries. Each layer of print is generally 50 microns thick. Individual layers of powder and binder are printed until we can create a unique and precise 3D part.
- After the print is complete, a cure operation is required to provide enough green strength for the part to be handled. This is achieved by heating the binder to a temperature of a couple hundred degrees Celsius. The finished part is loaded into a cure oven.
- When the cure is complete, the de-powdering operation begins. All loose powder is removed from the part, so it won’t be sintered into the final product. This labor-intensive operation is completed using brushes and compressed air. DSB is looking to leverage its internal automation group to automate this process to decrease manual labor requirements and increase quality of the operation.
- Once the part has been de-powdered, it’s ready for sintering. An important consideration in metal binder jet design is sinter shrinkage; a 20% decrease in size is typical, and similar to what occurs in metal injection molding. Our vacuum furnace provides high-temperature sintering in a continuous process.
- After the part has been sintered to its desired material properties, it can be shipped to the customer or undergo additional manufacturing if required. Our secondary machining department is capable of extensive post-sinter manufacturing including milling, turning, tapping, and more. If other specific post-sinter operations are needed, DSB can develop them in-house.
Metal binder jetting accelerates production development, allowing DSB to proceed from design to a sintered part in about one week. That’s what makes DSB your one-stop metal binder jetting manufacturing partner!
Understanding Metal Binder Jetting Technology
Design Features
Explore & learn more about Metal Binder Jetting design features and possibilities. A practical and functional 3D printing solution.
Prototyping
Explore & learn about Metal Binder Jetting prototype service. A 3D-print complex metal parts with nearly limitless design freedom.
Resources
Optimize your part design for Metal Binder Jetting with highly complex geometries, unique features, greater surface finish, and no tooling.