What is Sintering?
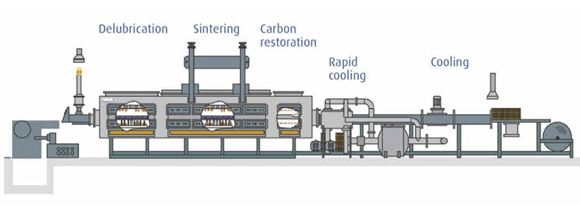
Sintering is a heat treatment for bonding particles in a solid state that is applied to a powder compact to increase a component's strength and integrity.
After compaction, neighboring powder particles are held together by cold welds, which give the compact sufficient “green strength” to be handled. At sintering temperature, diffusion processes cause necks to form and grow at these contact points.
Diffusion of atoms from one particle to another and between elements progresses at higher rates with increased temperature. The closer to the melting temperature of the material, the faster the sintering process progresses - and the better the final material properties.
DSB Technologies: Your Sintering Expert
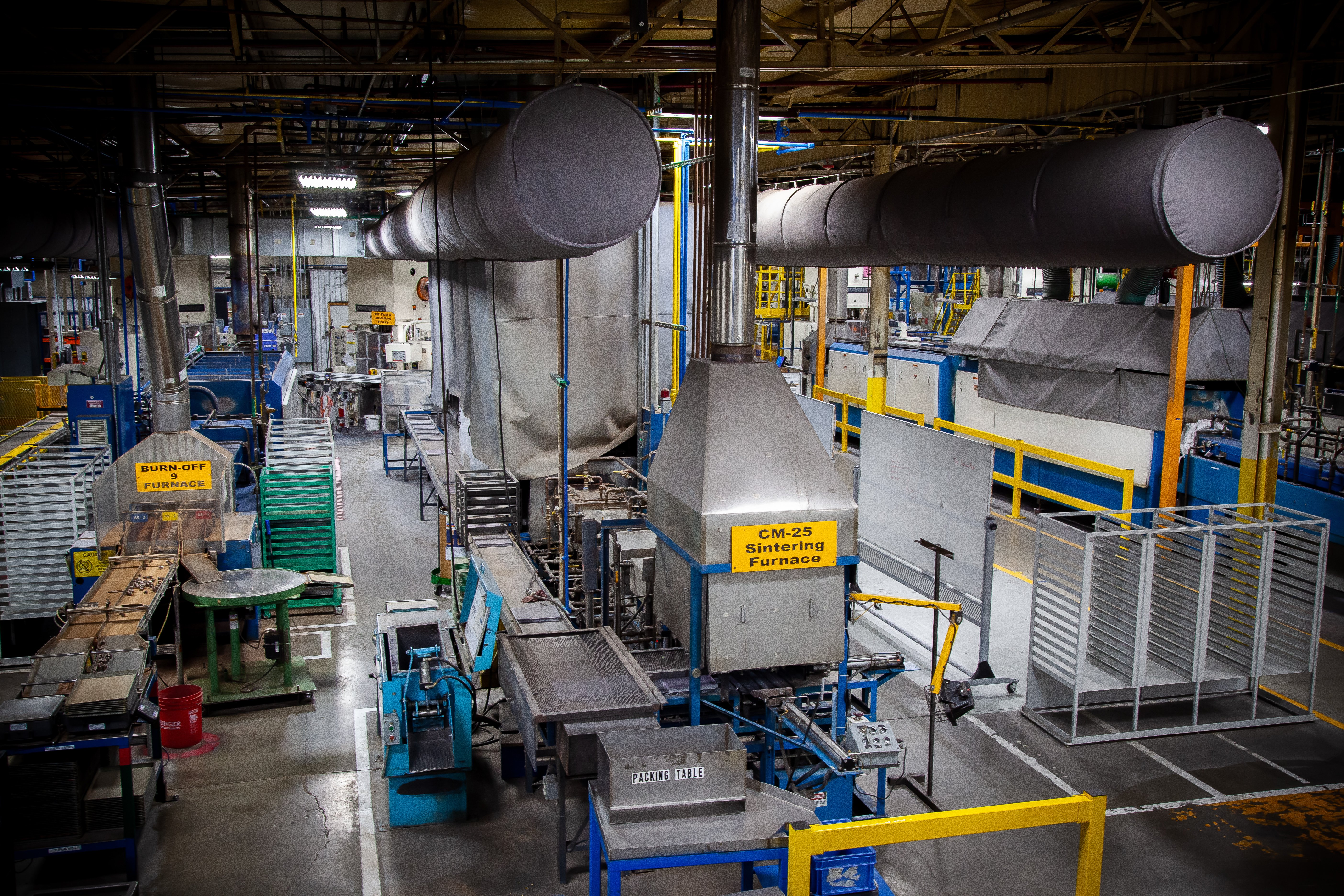
High volume production of high-performance metal parts requires both breadth and depth of sintering knowledge combined with the capacity to maintain efficient operations.
The sintering process's complexity is fixed on the ability to control shrinkage and dimensional control. Through years of development in dimensional control of sintering, DSB Technologies is the metallurgical partner for industrial manufacturers with volume production targets who need the power of sintering without the risk of development bottlenecks.
DSB Technologies delivers unrivaled expertise, as well as state-of-the-art technology, to bring about effective outcomes for three powder metal forming technologies: press and sinter, metal injection molding, and metal 3D printing.
The Sintering Processes Explained
Conventional Sintering
Conventional sintering is the standard practice of sintering uniaxial compacted PM components in metal belt conveyor furnaces. The maximum temperature is defined by the equipment capabilities; specifically the life of the metal muffle and metal belt. This maximum temperature is roughly in the range of 2050 F to 2150 F (1120 - 1180 C).
Materials & Benefits
The maximum temperature for conventional sintering can provide useful physical and mechanical properties for structural components in iron and low alloys steels, stainless steels, brass, bronze, copper, and aluminum. Many applications benefit from improved mechanical properties and moderate corrosion resistance with conventionally sintered 316 stainless steel. Process benefits for conventional sintering include: low material waste, solid dimensional control, and net shape or near net shape final dimensions.
High Temperature Sintering
While conventional sintering provides useful physical and mechanical properties, high temperature allows for optimum properties. Higher sintering temperature and time at temperature leads to more mass transport, more rounded residual pores, stronger bonds between particles, and greater densification. This enables better mechanical, physical, and magnetic properties.
Materials & Benefits
High temperature sintering (HTS) is particularly beneficial for stainless steels where densification occurs to reach non-interconnected surface porosity, greatly enhancing corrosion resistance - even exceeding that of comparable wrought steels. Also, ductility and toughness are improved with HTS in low alloy steels containing chromium, similar in composition to 4140 steel. Process benefits for HTS include improvements in corrosion resistance, high temperature oxidation resistance, ductility and toughness.
Liquid Phase Sintering
Conventional and high temperature sintering typically occur entirely in the solid state. With liquid phase sintering, some portion of the compact melts during the process while some portions remain solid. The solid portion maintains the shape of the compact while the portion that becomes liquid leads to particle rearrangement and densification.
Materials & Benefits
Liquid phase sintering is an important mechanism for the densification to near full density of tool steels such as M2 and T15. Tungsten heavy alloys such as tungsten-nickel-iron (radiation shielding) and tungsten-copper (thermal management) rely on liquid phase sintering for densification, as well as the cemented carbides for cutting tools (tungsten carbide-cobalt). Liquid Phase Sintering poses benefits for tool steels, which can reach near full density to achieve wrought-like properties for high performance applications.
Powder Metal Sintering Resources
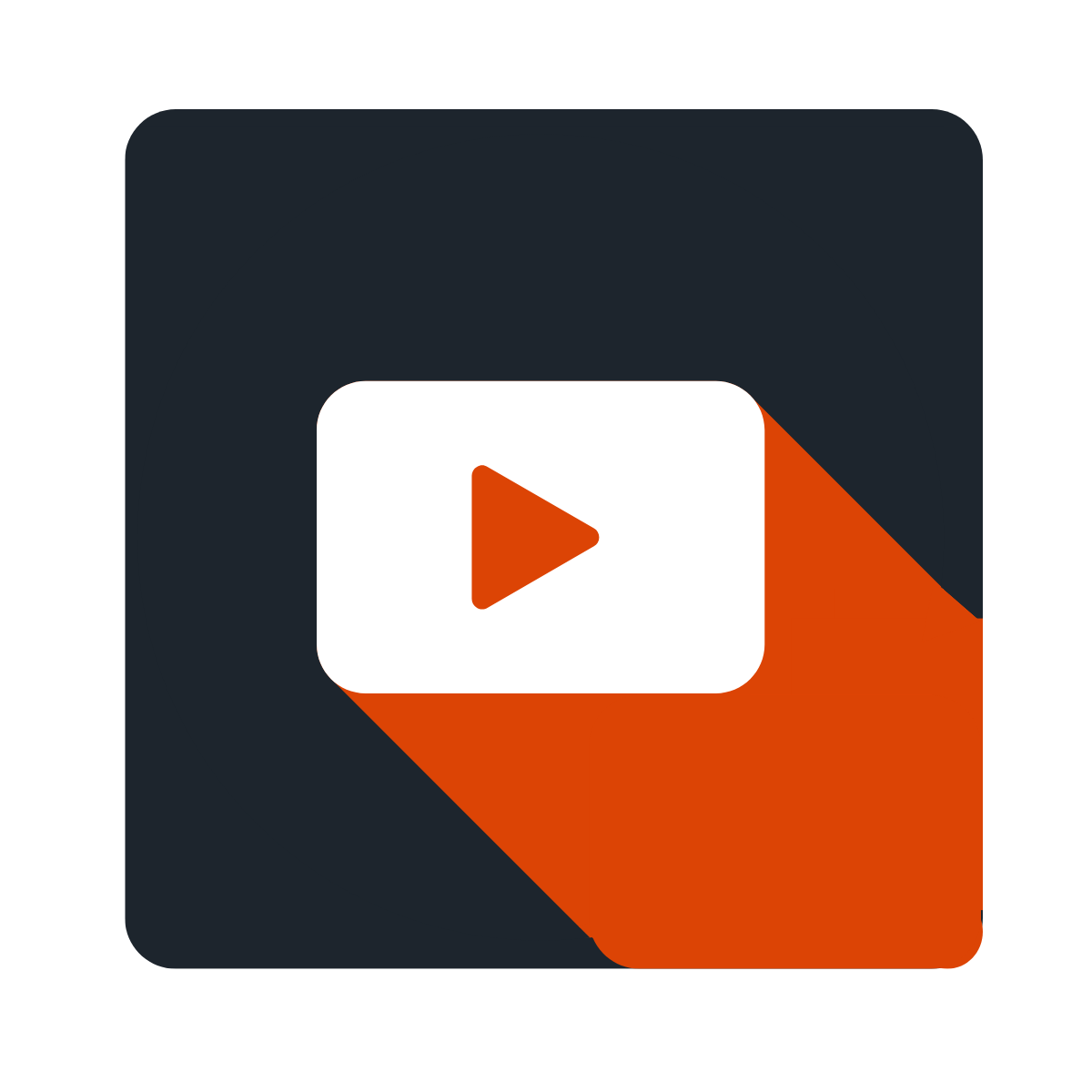
Sintering in Powder Metallurgy
Learn how conventional and high temperature sintering impact common PM material groups like Stainless Steels, Soft Magnetic Alloys, and Low Alloy Steels.
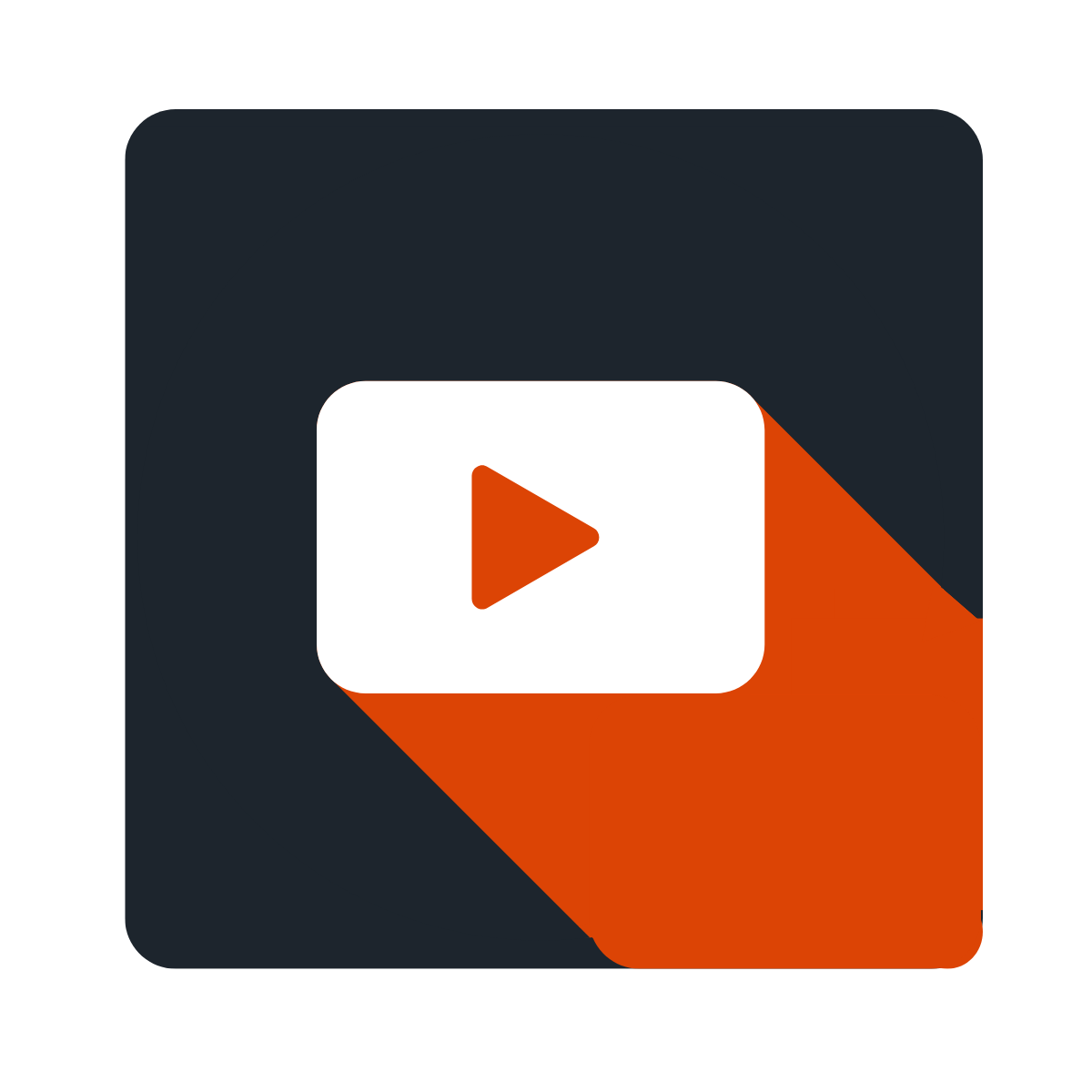
Sintering in Metal Injection Molding
Join DSB's MIM experts to explore best practices associated with high temperature sintering for Metal Injection Molding.
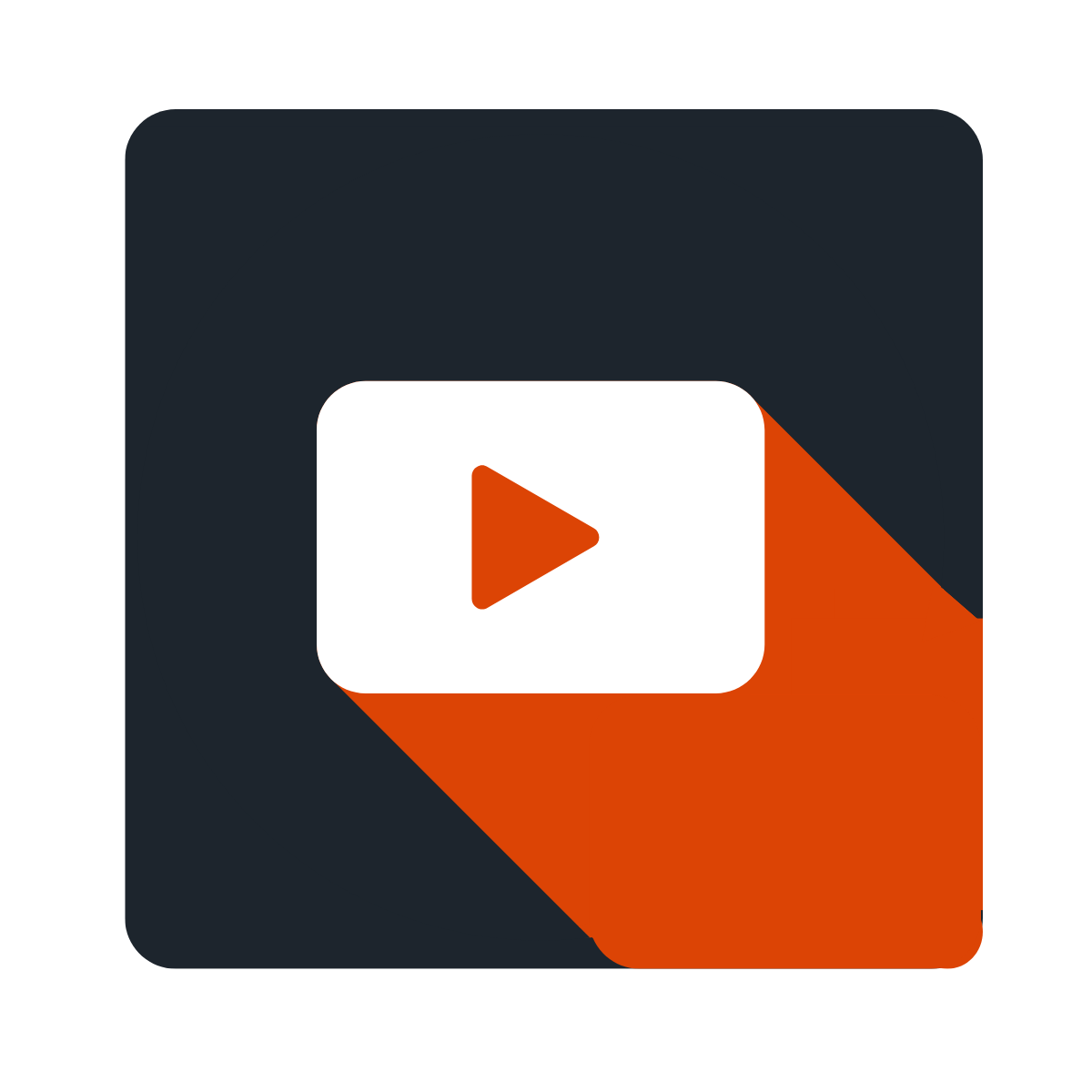
Sintering in Additive Manufacturing
Different from other manufacturing methods, learn how to sinter for Metal Binder Jetting.
Metal Sintering FAQ
What are the benefits of metal sintering?
What are the benefits of metal sintering?
Metal sintering offers several benefits that make it a valuable manufacturing process across various industries. Some of the key advantages of metal sintering include: complex geometry, material utilization, near net shape manufacturing, cost-effectiveness, material variety, high dimensional accuracy, customization and more
How strong is sintered metal?
How strong is sintered metal?
The strength of sintered metal parts can vary depending on several factors, including the specific metal powder used, the sintering process parameters, and the part's geometry and design. Generally, sintered metal parts exhibit good strength properties, but the exact strength levels can vary depending on these factors; density, material composition, sintering process parameters, microstructure, post-sintering treatment.
Sintering vs Melting: what is the difference
Sintering vs Melting: what is the difference
Melting:
-Melting involves heating a material, typically a metal, to its melting point, causing it to change from a solid to a liquid state.
-In this liquid state, the material can be poured or cast into molds to form desired shapes.
-After cooling and solidification, the material retains its new shape and properties.
Sintering:
-Sintering is a process used to bond particles of a material together without melting them completely.
-It involves heating the material to a temperature below its melting point but high enough to cause atomic diffusion and bonding between particles.
-Sintering is commonly used with powdered metals and ceramics to create solid objects with desired shapes and properties.
-During sintering, the particles are fused together, but they do not reach a fully molten state.
Are DMLS and SLS the same?
Are DMLS and SLS the same?
SLS uses a laser to sinter a plastic powder into a part. DMLS, on the other hand, uses a high-powered laser to sinter metal powder into a high-performance part.
What is powder bed fusion?
What is powder bed fusion?
Powder bed fusion (PBF) is a subset of additive manufacturing (AM) whereby a heat source (eg, laser, thermal print head) is used to consolidate material in powder form to form three-dimensional (3D) objects.
What is sintering?
What is sintering?
Sintering is a process where metal particles are heated to bond them together without melting.
What materials benefit from conventional sintering?
What materials benefit from conventional sintering?
Iron and low alloy steels, stainless steels, brass, bronze, copper, and aluminum.
What is high temperature sintering?
What is high temperature sintering?
It uses higher temperatures to enhance mechanical, physical, and magnetic properties.
What is liquid phase sintering?
What is liquid phase sintering?
A process where some portion of the compact melts, aiding particle rearrangement and densification.
What industries use sintering?
What industries use sintering?
Aerospace, automotive, medical, consumer goods and more!
How does sintering improve material properties?
How does sintering improve material properties?
Enhances density, strength, and durability of metal parts.
What are the typical applications of sintered parts?
What are the typical applications of sintered parts?
Gears, bearings, filters, and structural components