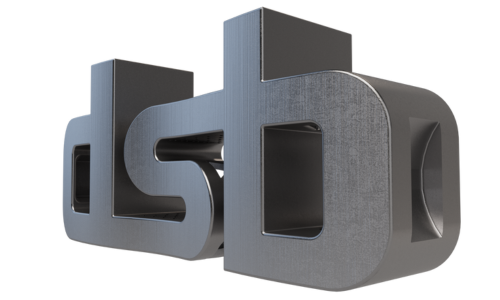
Designing for Metal Binder Jetting
With the 3D design of the DSB logo, explore the possibilities of designing metal parts with highly complex features through a cost effective Metal Binder Jetting solution.
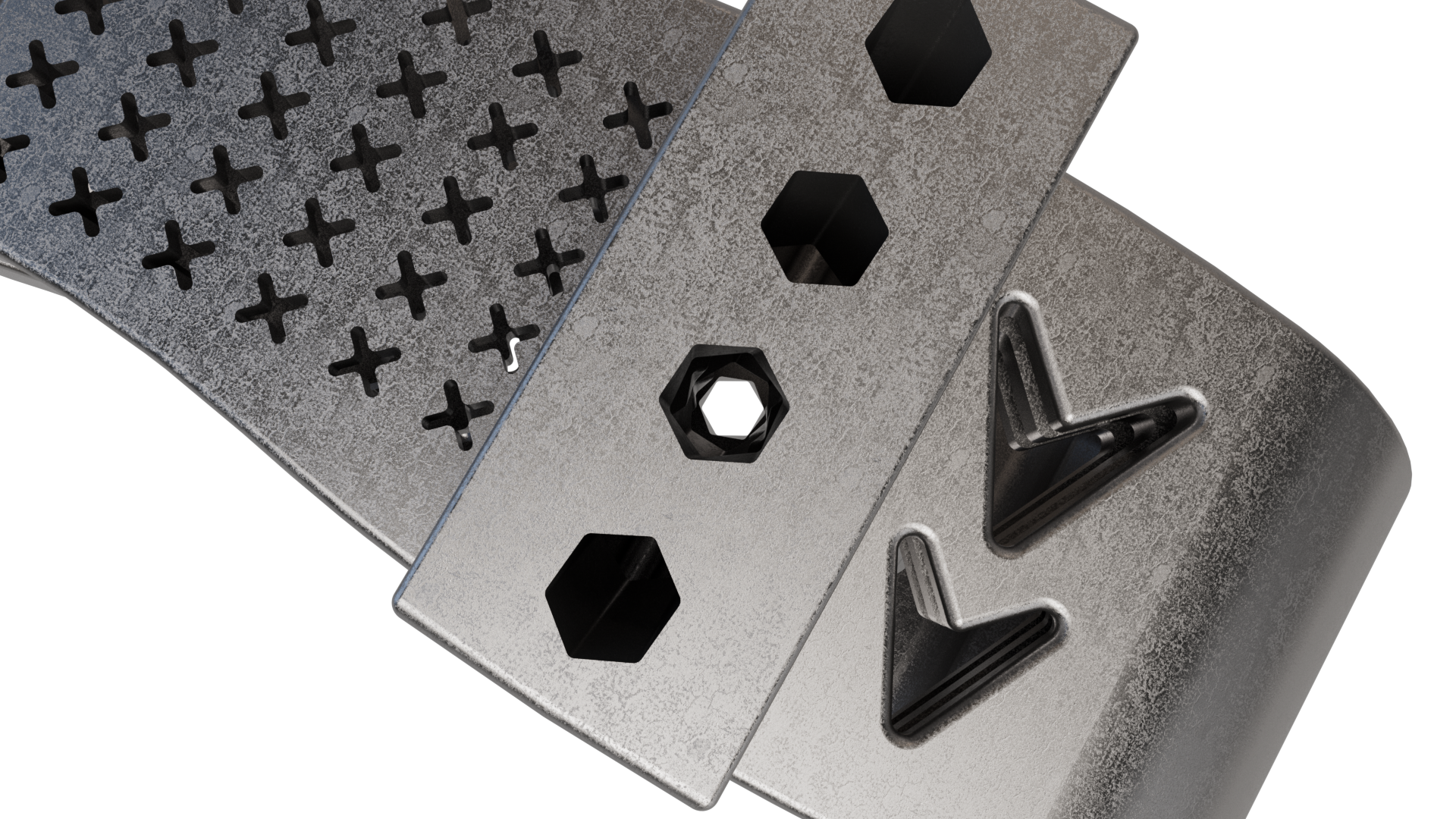
Metal Binder Jetting Prototyping
In a race to the market, speed wins. Create and iterate metal parts with nearly limitless design freedom in four weeks or less with DSB's Metal Binder Jetting Prototyping.
Metal Binder Jetting Advantages
Geometric Freedom
Because of the process's capabilities to support parts through sintering and control distortion, Binder Jetting allows for design freedom to create undercuts, complex internal channels, lattices, sharp edges and corners, surface textures, and fine features.
Printing Speed
Binder Jetting print speeds are much faster than competing additive processes, opening the door for the possibility of higher volumes and more cost-competitive finished parts.
Part Accuracy
To ensure part accuracy, we have the ability to manage shrinkage during sintering. Also, post-sintering secondary operations can support qualifying key dimensions and addressing surface finish requirements.
Thinner Wall Thickness
Thinner wall thicknesses aid in the removal of the binder prior to sintering, and more uniform wall thicknesses minimize the potential for distortion and cracking during sintering.
No Tooling
With the ability for iterative design changes in a single build, Binder Jetting eliminates the need for expensive upfront tooling costs and retooling - significantly reducing lead times.
Reduced Support Structures
Binder Jetting minimizes the support structures needed by using the powder bed itself to support the part while printing. Sinter support structures can also be printed at the same time - separate from the part - to reduce the need for support structure removal after printing and sintering.
Internal Geometries
Binder Jetting excels at producing parts with internal geometries as the powder acts as the support structure to the internal cavities and is easy to remove as long as there is some open passageway to the surface.
Light-Weighting
Binder Jetting supports light-weighting not only by controlling the fill ratio through lattice structures, but also by providing a porous initial structure that can be sintered to maintain the porous structure, infiltrated to create a composite structure, or sintered to high density.
Metal Binder Jetting: A realistic method for 3D printing in volume production
How it works:
An industrial printhead selectively deposits a liquid binding agent onto a thin layer of metal powder particles to build high-value and one-of-a-kind parts and tooling. The process is repeated layer by layer, using a map from a digital design file, until the object is complete. Metal materials are cured and sintered after printing to achieve densities greater than 97%, in line with metal injection molding (MIM) and better than investment castings.
Your Manufacturing Partner for Industrialized Metal Binder Jetting
Industrialized 3D Printing Systems
Desktop Metal® X-Series Metal Binder Jetting Print Systems: InnoventX, X25Pro, and X160Pro—The world’s largest binder jet 3D printer.
In-House Metallurgy Processes
Advanced Manufacturing Lab + 250,000 sq ft facility of additional metallurgical operations.
Sintering Capacity
The largest capacity of continuous high temperature sintering in North America with 32 HT furnaces.
Available Materials
Current material availability includes 17-4 PH Stainless Steel, 316L Stainless Steel, M2 Tool Steel and 4140.
Production Portfolio
In-house printing, sintering, secondary machining, and automation to drive volume production in MBJ.
Metal Additive Manufacturing Resources
Understanding Metal Binder Jetting Technology
Design Features
Explore & learn more about Metal Binder Jetting design features and possibilities. A practical and functional 3D printing solution.
Prototyping
Explore & learn about Metal Binder Jetting prototype service. A 3D-print complex metal parts with nearly limitless design freedom.
What is it?
What is Metal Binder Jetting? Metal Binder Jetting is used to create designs with nearly limitless 3D possibilities.
Metal Binder Jetting FAQ
What is the binder jetting process?
What is the binder jetting process?
Binder jetting is a method of additive manufacturing where a specialized printhead precisely applies a liquid binding substance onto a fine layer of powder particles, including materials like foundry sand, ceramics, metals, or composites. This process is utilized to construct unique and high-quality parts and tooling.
How accurate is metal binder jetting?
How accurate is metal binder jetting?
Metal binder jetting delivers exceptional precision, crafting intricate shapes and fine details. Through meticulous calibration, control, and parameter optimization, it attains tight tolerances and accuracy, making it applicable across diverse industries such as aerospace, automotive, and healthcare.
What can metal binder jetting be used for?
What can metal binder jetting be used for?
Metal binder jetting can be used for a variety of applications across different industries. Some common uses include:
Prototyping: Rapid prototyping of metal parts for design validation and iteration.
Tooling: Production of custom tooling and fixtures used in manufacturing processes.
Customized Components: Manufacturing of complex, custom metal components with intricate geometries.
Small Batch Production: Cost-effective production of small batches of metal parts without the need for expensive tooling.
Aerospace: Manufacturing lightweight, high-strength aerospace components such as brackets, heat exchangers, and engine parts.
Automotive: Production of automotive components including engine parts, brackets, and customized interior features.
Medical: Fabrication of medical implants, surgical instruments, and patient-specific prosthetics.
How does metal binder jetting work?
How does metal binder jetting work?
Metal binder jetting is an additive manufacturing process that involves several key steps:
Powder Preparation: The process starts with a thin layer of metal powder spread evenly over the build platform.
Binder Application: A print head selectively deposits a liquid binding agent onto the powder bed. This binder serves to bond the metal particles together in the desired pattern.
Layer-by-Layer Build: After the binder is applied, another layer of metal powder is spread over the previous layer, and the process is repeated. This layer-by-layer approach allows for the gradual buildup of the desired part.
Drying and Curing: Once each layer is deposited, it may go through a drying and curing process to solidify the binder and strengthen the part.
Sintering: After the entire part is printed, it undergoes a post-processing step called sintering. Sintering involves heating the part to a temperature just below its melting point, causing the metal particles to fuse together. This step imparts strength and density to the part.
Additional Finishing (Optional): Depending on the application, additional finishing steps such as machining, polishing, or surface treatments may be applied to achieve the desired surface finish and dimensional accuracy.
Through this process, metal binder jetting enables the production of complex metal parts with high precision and relatively short lead times compared to traditional manufacturing methods.
Can metal binder jetting be used to create customized or personalized parts?
Can metal binder jetting be used to create customized or personalized parts?
Yes, metal binder jetting can be effectively used to create customized or personalized parts. Here's how: design flexibility, personalized features, variable geometry, mass customization, rapid prototyping, on-demand manufacturing and digital design integration
What are the advantages of metal binder jetting?
What are the advantages of metal binder jetting?
It allows for geometric freedom, fast printing speeds, part accuracy, thin wall thickness, no tooling, reduced support structures, and internal geometries.
What materials are used in Metal Binder Jetting?
What materials are used in Metal Binder Jetting?
17-4 PH Stainless Steel, 316L Stainless Steel, M2 Tool Steel, and 4140.
What is the printing speed of Metal Binder Jetting?
What is the printing speed of Metal Binder Jetting?
Faster than competing additive processes, enabling higher volumes and cost-competitive parts.
How does Metal Binder Jetting handle support structures?
How does Metal Binder Jetting handle support structures?
Minimizes support structures using the powder bed and can print sinter support structures separately to reduce post-processing.
Is Metal Binder Jetting suitable for light-weighting parts?
Is Metal Binder Jetting suitable for light-weighting parts?
Yes, through lattice structures and controlling the fill ratio, it supports light-weighting.
How long does Metal Binder Jetting Prototyping take?
How long does Metal Binder Jetting Prototyping take?
The time it takes to complete a metal binder jetting prototyping project can vary depending on several factors, including the complexity of the part, its size, the layer thickness used during printing, the equipment's printing speed, and post-processing requirements. Generally, metal binder jetting prototyping projects can take anywhere from a few hours to several days or even weeks to complete.