Injection Molding Products
Injection molding is a prime manufacturing process that involves injecting molten material into a mold cavity under high pressure, empowering the rapid production of different parts. While primarily associated with plastics, injection molding can also be applied to metal products through the process of metal injection molding (MIM).
DSB Technologies leverages an innovative 3DM approach to the MIM process, utilizing a new low-shrink feedstock and automated molding techniques to produce larger, complex metal parts exceeding 100 grams. This advancement reduces part variability and improves dimensional stability, allowing for more efficient, high-volume production of strong metal components.
Understanding Injection Molding
Injection molding is used to produce parts by injecting molten material into a mold. It's widely used for mass-producing plastic parts, though it can also be used with some metals.
The basic process:
- Injection: Molten material is injected into a mold cavity under high pressure.
- Cooling: The material cools and solidifies within the mold, taking its shape.
- Ejection: Once cooled, the part is ejected from the mold.
The Metal Injection Molding (MIM) Process
Metal Injection Molding (MIM) is a manufacturing process that combines the versatility of plastic injection molding with the strength and integrity of metal parts. It involves mixing fine metal powders with a binder to create a feedstock, which is then injected into a mold cavity. After molding, the binder is removed, and the part is sintered to achieve its final properties.
Traditional metalworking vs. MIM:
- Complexity: MIM can produce more complex geometries than traditional methods like machining or casting.
- Material usage: MIM typically has less waste compared to subtractive processes like machining.
- Production volume: MIM is more cost-effective for medium to high volume production runs.
- Finishing: MIM parts often require less post-processing than traditionally manufactured parts.
MIM is particularly useful for producing small, intricate metal parts in industries such as automotive, medical devices, and consumer electronics. It bridges the gap between the shape complexity of plastic injection molding and the material properties of metals.
Common Products Made with Injection Molding
Numerous plastic and metal goods can be crafted from injection molding. Its ability to create complex shapes with high precision and speed has made it the go-to method for producing a wide range of products.
Here are some common categories of plastic products typically made using injection molding:
- Household items
- Containers, toys, and kitchen tools
- Industrial components
- Gears, brackets, and housings
- Automotive parts
- Dashboard components, trim pieces, and under-the-hood parts
Metal Injection Molding (MIM) has expanded the possibilities of metal part production, allowing for the creation of complex, precise components across various industries. This process combines the design freedom of plastic injection molding with the strength of metals.
Here are some common categories of metal products typically made using injection molding:
- Automotive parts
- Engine components, transmission parts, steering system components
- Electronics
- Connectors, housings, internal components
- Medical devices
- Surgical instruments, implants, diagnostic equipment parts
Industries benefiting from MIM include:
- Aerospace
- Automotive
- Consumer electronics
- Healthcare and medical devices
- Firearms
- Industrial machinery
- Jewelry
- Sporting goods
MIM's ability to produce intricate metal parts with high precision and consistency makes it invaluable in these sectors. The process allows manufacturers to create components that would be difficult or impossible to produce using traditional metalworking methods, often at a lower cost and with less material waste.
Injection molding stands at the forefront of modern manufacturing, demonstrating remarkable versatility across both plastic and metal applications. This process has revolutionized production capabilities, enabling the creation of complex, precise, and consistent parts at scale.
Whether you're a seasoned user of these technologies or considering them for future projects, DSB can help make your goals a reality. Get in touch with us today to learn more about our MIM technology!
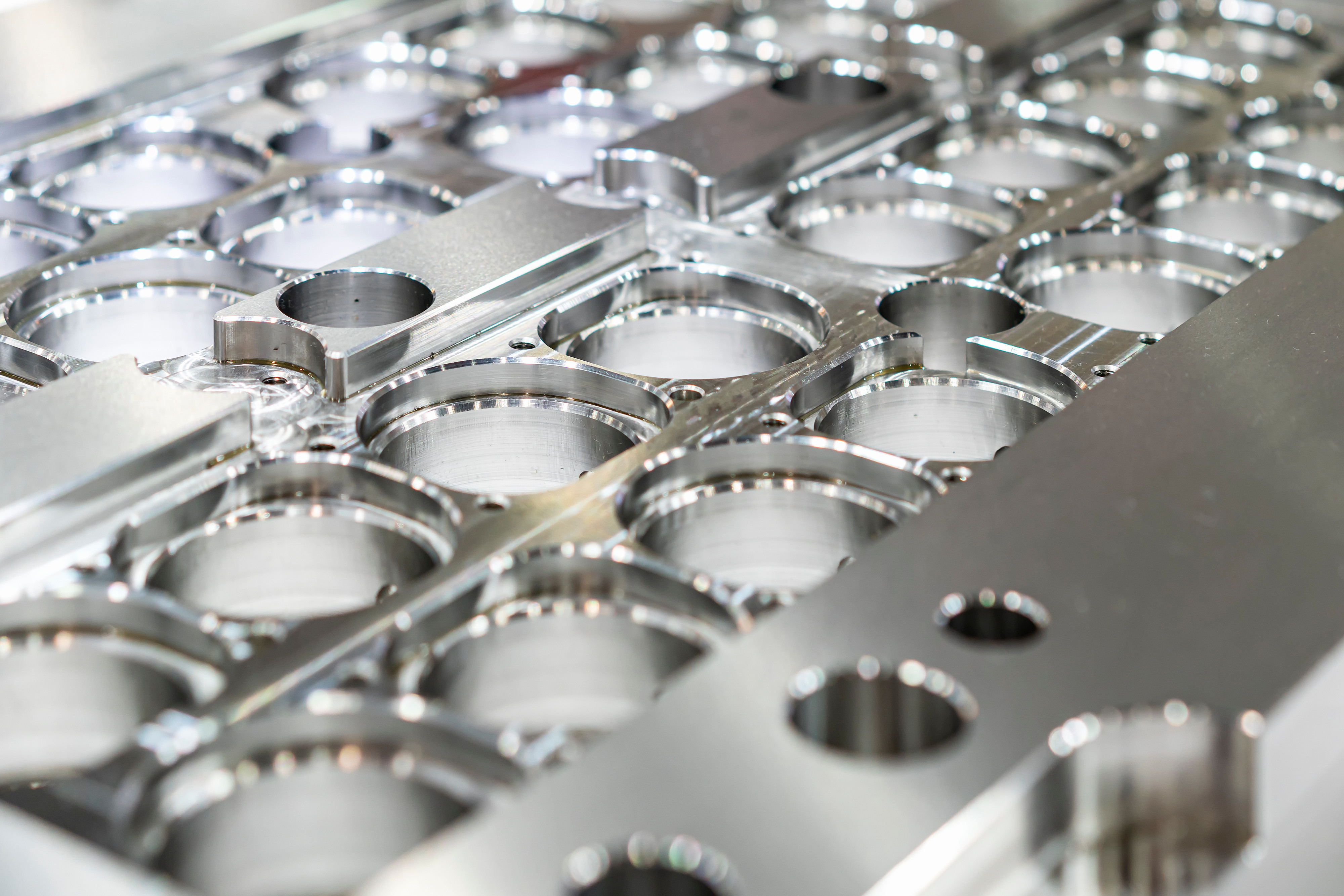
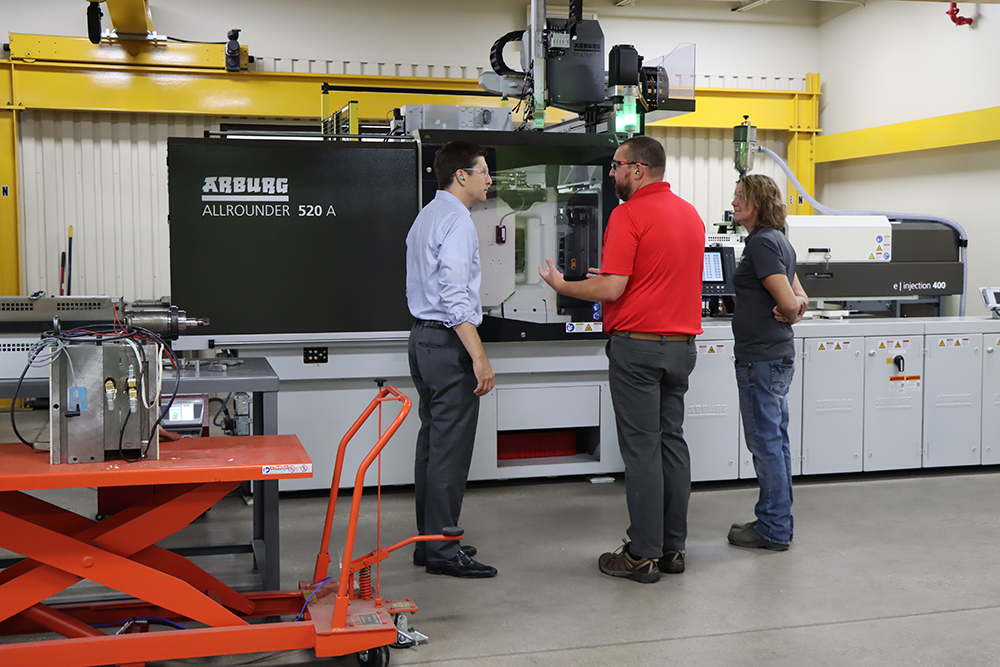